Resources - Siphon breaks
What are they, how do they work and what happens if they are not there?
Chapter 2
The idea behind a dippipe is that you can unload a pressurised tank from a pipe that leads out of the top of the vessel. This has an advantage that it can reduce the number of places in a pressure vessel that has a hole cut through it and also it means that if you have very limited access to the lower half of a tank, you can do everything from the top.
Pressure vessels are expensive and many are reused that is how you can end up with a pressure vessel that has a dippipe in a situation where you should not have one, like the Ethylene Oxide and Propylene Oxide tanks padded to 3 Bar pressure with nitrogen, on the plant in the book.
Comparison of how tanks with and without a siphon break modification on pre-existing dip-pipes work under various conditions. |
Dippipe modified with siphonbreak |
|
Dippipe not modified |
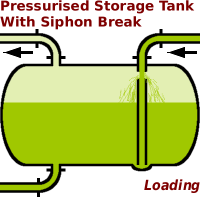
The disadvantage of toploading liquid into a partially pressurised tank is that some of the padding gas (in this case nitrogen) dissolves in it this will happen whether you are looking at a dippipe tank with a siphonbreak or with a normal loading pipe that goes into the top of the tank.
In the case of the dippipe with the siphonbreak, you can get padding gas being entrained with the liquid being loaded as virtually all of it flows down the dippipe to the bottom of the vessel, or, you can get liquid hitting the side of the siphonbreak holes and spraying out into the vessel, picking up padding gas on the way depending on: flowrates; viscosity; pipe diameter; levels; the shape of the delivery pipework just before it enters the vessel; and, so on. |
|
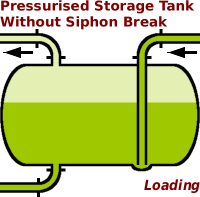
The surface is not broken thus there is no opportunity for the padding gas to dissolve into the liquid that is being loaded, other than would normally take place once loading had finished, with the obvious exception of the fact that the concentration of padding gas in the liquid will be lowered as the liquid moves around as the tank is filled.
With loading, one important disadvantage is that should the loading line fail, the tank can empty out again, through the loading line, all over the lorry or wherever the failure is. Simple oneway valves are all that are needed to cure this but remember that trusting a oneway valve is more of an act of faith than anything else and you should have another plan as they fail notoriously easily.
|
|
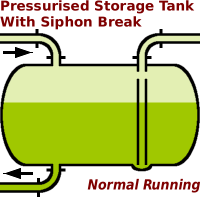
Everything is just hunkydory.
|
|
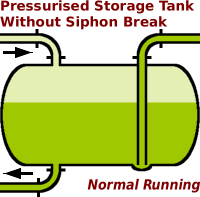
As far as the plant is concerned, it all runs all right.
The disadvantage as far as safety is concerned is that you have pressurised liquid going towards the tanker unloading bay (obviously, you have a valve somewhere) all of the time that the plant is running and there is no unloading happening the unloading bay, therefore, is not manned thus, if anything goes wrong, it is less likely to be noticed at the time.
A further consequence of that is that you can end up with betweenvalve lengths of pipe that have only liquid in them therefore any S.O.P. should include blowingout the pipes after unloading. However, that is yet another source of fugitive emissions. |
|
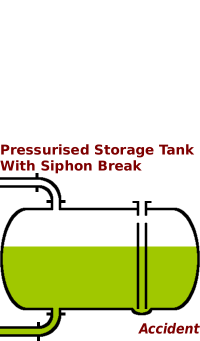
Pressurised gas escapes to atmosphere, leaving the liquid in the tank.
Once the pressure has equalised, the only escapes from the tank will be as a result of dissolved padding gas coming out of solution and taking vaporised liquid or droplets of liquid with it, as it escapes through the siphonbreaks and out through the broken pipe.
Another way that gas and vapour/liquid droplets can escape is that when the tank depressurised, the gas inside cooled down adiabatically and therefore is quite cold. As it heats up, it will expand, pushing out the vapour/droplets with it.
It probably pays to be aware that there will still be vapour leaking from the tank once it has depressurised and that it will probably be flammable as well if a flame gets inside the tank, you can end up with an explosion if the flammable chemical has no upper explosive limit, such as Ethylene Oxide. |
|
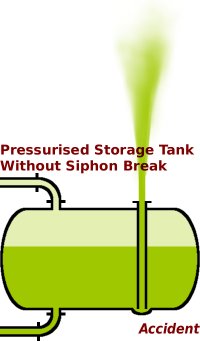
Despite having the inlet pipe knocked off completely, the tank remains completely pressurised and will remain so unless steps are taken to do something about it such as vent it through another pipe.
At 3 bar (gauge), a tank that is slightly over two thirds full (almost three quarters, depending upon how far above the piping failure is from the surface of the liquid in the tank) will empty completely through the dippipe if no steps are taken to reduce the gas pressure in the tank. |
Siphonbreaks on dippipes therefore are a must. Having them on the plant flowsheets but not on the actual plant is fraud.
|  | Could it really be, I thought, that Snaiths management style was in fact considered by his superiors to be a splendid example of how the human resources department should be run in real life? |  |
Copyright © 1994-2023 James F Linden. All Rights Reserved.
|